エネオスにおいてCO2とH2からの炭化水素からの合成パイロットプラントについては前にも書いたが、次は茨城県つくば市の産業技術総合研究所が二酸化炭素(CO2)と水から合成燃料を一貫製造する新しい設備を開発し、メディアに公開した。分解から合成まで一貫して製造する設備であり、流動接触分解をうまく取り入れている。個人的なことだが ガイドを読んでるうちに懐かしい設備名が出て来たのがうれしかった。おじさん製油所でトッパーと言う蒸留装置の担当の次がFCCと呼ばれた流動接触分解部門に関わったので 懐かしく読んでしまった。
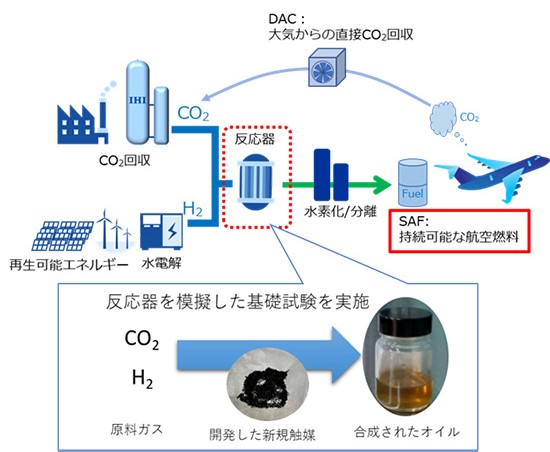
ヨーロッパで言われたE―FUELについて書いた時も書いたが、昔から日本に入ってくる原油自体が 硫黄が多く重質分が多いB品だったので、白油化(軽質留分 軽油・灯油・ガソリンなどを多くする)とのテーマが常に業界の目標にあった。つまり 軽油・ガソリンなどを作り出すための分解・改質設備 あるいは公害防止から脱硫と言うプラントが日本では進化した。メジャーと呼ばれた原油供給大手の「くびき」が存在する石油業界ならではである。従って日本の石油業界には 昔からプラントの運転に慣れた経験者が多く、新しく出来た製品の蒸留・保管などについても心配はいらない。日本の石油精製の創成期からの弱点補強策が功を奏しだす時代となったのである。
石炭火力発電の愛知県の碧南などにおけるCO2地下貯留など 高濃度の二酸化炭素を得ることも出来るようになってきた。また造船所によっては 二酸化炭素移送船などの建造も始まっている。後は効率向上の問題は残るが、いずれ改善されると見込める。
地球大気から二酸化炭素を集めることは非常に効率が悪い。二酸化炭素の大発生場所で集約・精製・濃縮することが最も効率が良い。少なくとも二酸化炭素の発生を管理しながら、その量を減らすことに意義がある。特に二酸化炭素は少しの変化で三態(気体・液体・個体)変化する性質があり、大量保管には注意を要する。
バイオ燃料と合成燃料を軸に 今から起きるであろう液体燃料革命の時代を見ることが出来そうである。おじさんが燃料会社を辞める前後から 東京ガスなどの天然ガスの輸入・都市ガスの転換が行われ、同時にC1化学と称されるメタンからの合成などが研究されていた。また重質留分と呼ばれる重油に近い成分を分解して、発生した軽質不飽和炭化水素を結合させアルキレートガソリンなどの製造・販売を始めた。分解・合成の研究と実運転プラントなどが作られ出した時代であった。
同時に 天然ガスを発電した際に出て来る熱エネルギーも利用するコージェネレーションシステムなどが小さなエリアで設置運営され、より効率化が計られた。 今回は 水とCO2から水素と一酸化炭素(CO)の合成ガスを作る装置と、その合成ガスから液体燃料を製造する設備を組み合わせた。分解から合成まで一貫して製造するため、従来より高効率だと思われる。エネオスなどの 水素を別途用意しないといけない合成燃料製造を一歩進めた形である。化石燃料に代わる次世代エネルギーとして製造コストの軽減に期待している。
次から次と 実証が溢れて来た!